Sustainability
Approach to the Environment
Environmentally-conscious Products
Contributing to measures against global warming with non-fluorocarbon product manufacturing around the globe
Chlorofluorocarbon (CFC) gas, which is used as a coolant and foaming agent, has a greenhouse effect of several thousand to several tens of thousands of times greater than carbon dioxide (CO2), and is known to be destructive to the ozone layer.
Crackdowns on CFCs are moving forward around the world, since April 2015, with Japan adopting the Act on Rational Use and Appropriate Management of Fluorocarbons (Revised CFC Act), which dictates stricter controls of CFCs.
Hydrofluorocarbons (HFC) have been used as a foaming agent to expand core materials in the insulated panel manufacturing process. Because such panels do not fall under the regulations and reduction controls of the Revised CFC Act, however, HFCs continue to be used.
Instead of using CFCs as a foaming agent, Nikkei Panel System is a forerunner in the industry establishing a non-fluorocarbon insulating panel manufacturing method that makes use of hydrofluoroolefins (HFOs), which have an extremely low impact on global warming and ozone layer destruction. Since April 2016, all of our panels are produced using this non-fluorocarbon method.
Note: Non-fluorocarbon insulated panel produced at Nikkei Siam Aluminium Ltd. (Thailand) use cyclopentane.
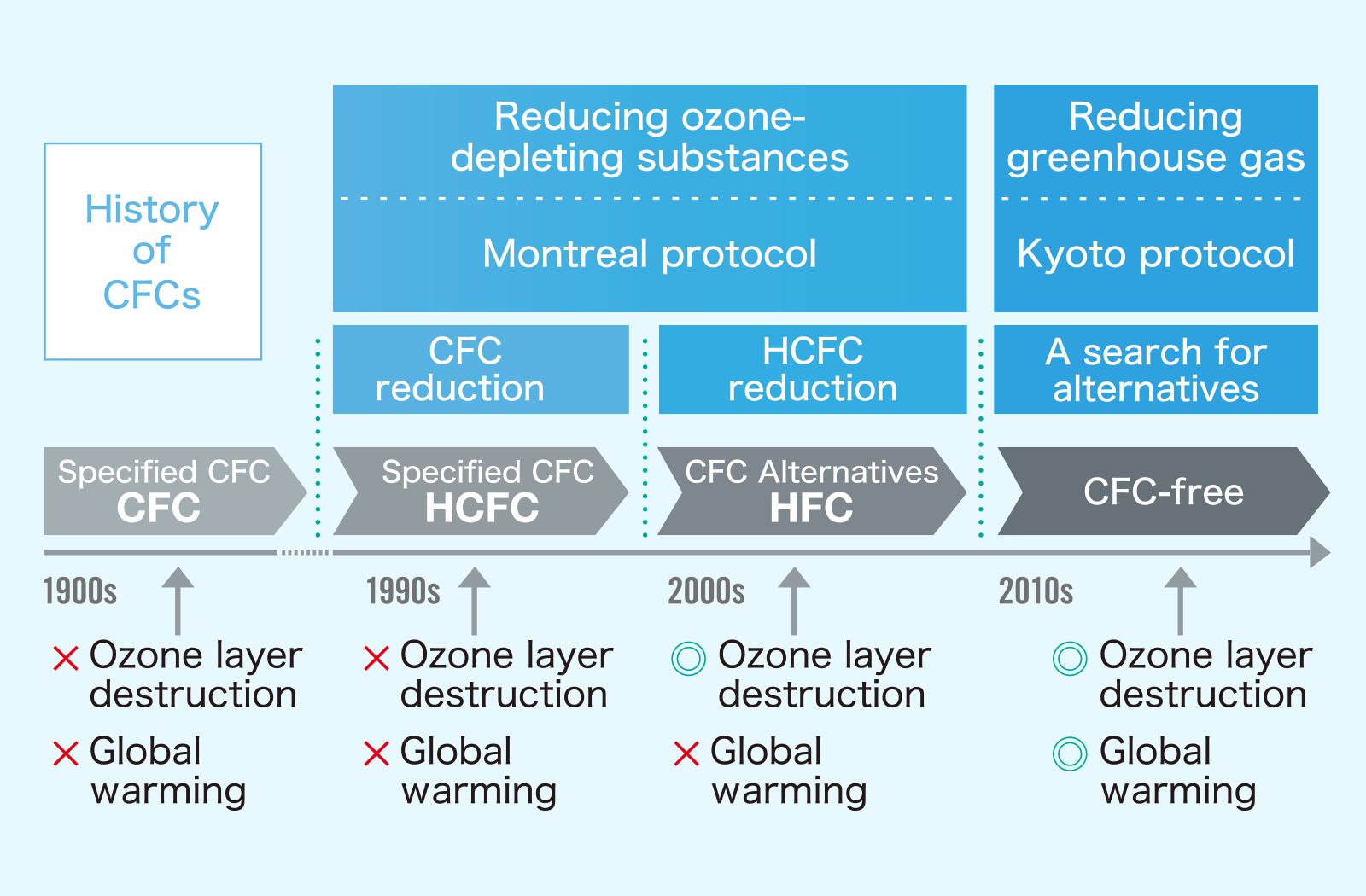
Adoption of non-fluorocarbon products achieves the same result as an annual reduction of nearly 300,000 tons of CO2
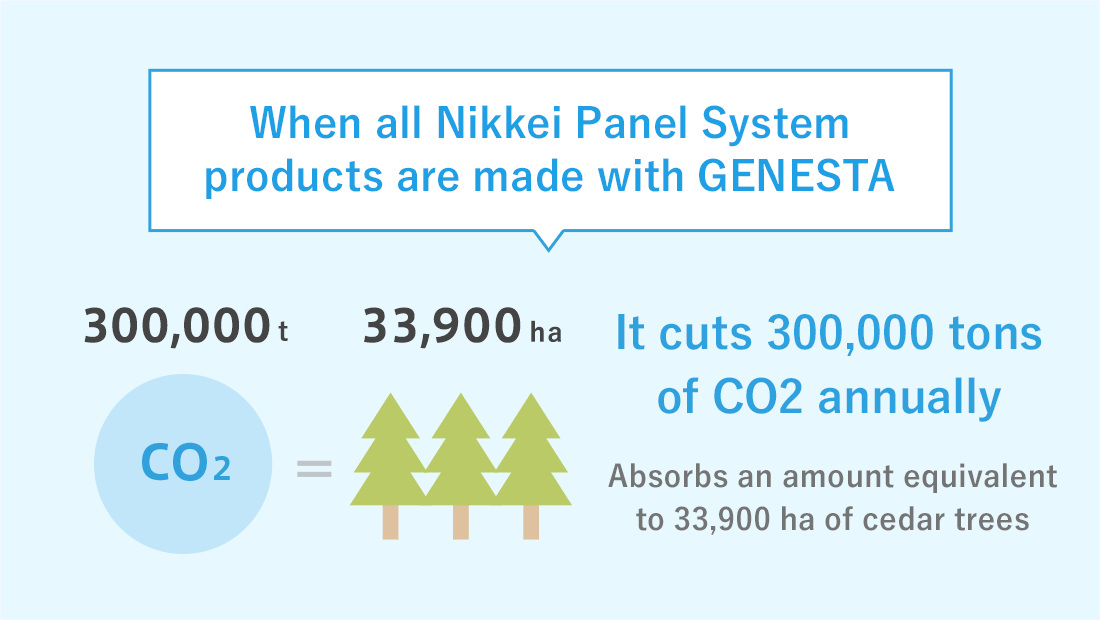
Switching to HFOs for all of our products made using HFCs should achieve the same result*1 as reducing 300,000 tons of CO2 annually.
When converted to the amount of CO2*2 absorbed annually by a single hectare of artificial cedar forest (40 years old), it achieves an effect equivalent to nearly 33,000 hectares of cedar trees (space equal to 7,200 Tokyo Domes, 5.3x the size of the area inside the Yamanote Line).
- Calculated based on our production volume from April 2013 to march 2014.
- A single hectare of artificial cedar forest absorbs approximately 8.8 tons of CO2 (From the Forestry Agency website).
Disaster-resilient Products
Developing new earthquake-resistant ceilings inspired by lessons learned from the Great East Japan Earthquake
The various spaces that we provide house irreplaceable things such as lives and assets.
Instead of simply building high-performance spaces, our goal is to develop products that are resilient in the face of and help mitigate disaster so that they can continue functioning as intended.
Such efforts began with the Great East Japan Earthquake in 2011.
During the earthquake, ceilings in many large spaces collapsed. This led to the revision of the Order for Enforcement of the Building Standards Act in April 2014, which included a standard*1 related to ceiling collapse measures, making compliance mandatory for all new structures. Even before the revision, we had begun to focus on the issue of collapsing ceilings, so we were successful in quickly developing the NEQRES earthquake-resistant ceiling series, which is compliant with the new standard.
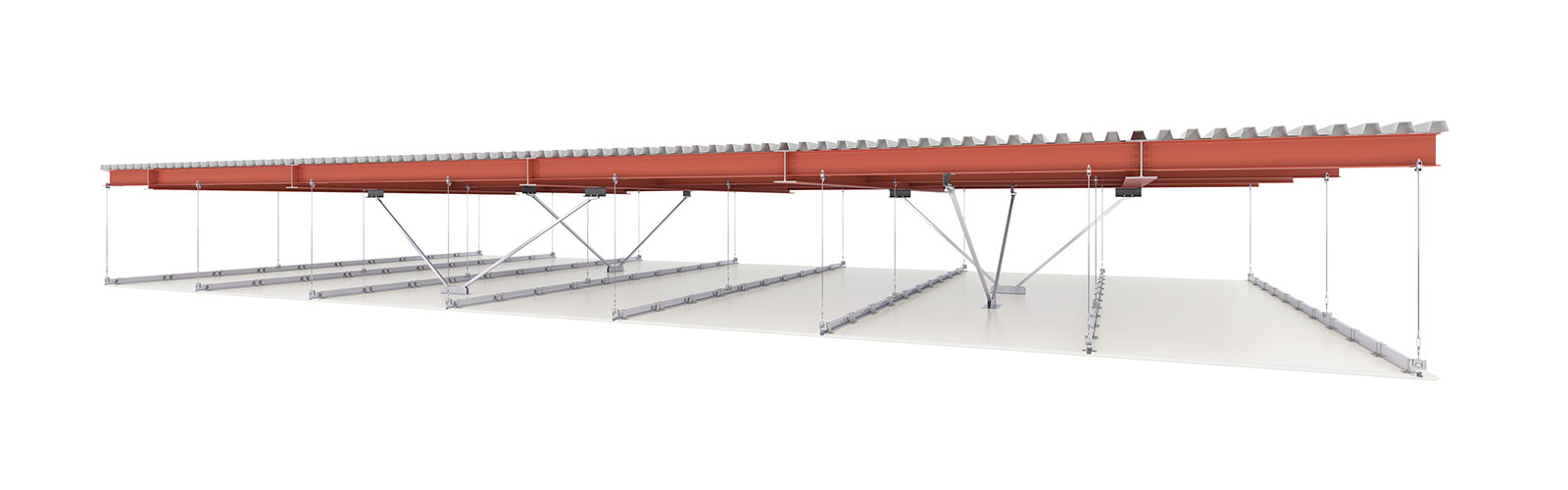
- Standard for specific ceiling type (drop ceiling with a height over 6 m, horizontal projection area over 200 m2, and mass per unit area of over 2 kg/m2, installed in a location used daily by people)
Renewable Energy Use
Generating the Tec Lab's annual power needs with rooftop solar panels at the Shiga Plant
The roof of the Shiga Plant Tec Lab is fitted with solar panels to generate power for the facility. It is estimated to generate the equivalent annual power consumed at the Tec Lab*1, helping cut CO2 emissions by approximately 50 tons per year.
Once the system began operation, a Nikkei Panel System licensed electrical engineer took charge of inspecting and maintaining the transformers and power conditioners.
- PPA (power purchase agreement) model: The facilities are installed and owned by the power company, from whom electricity is purchased.
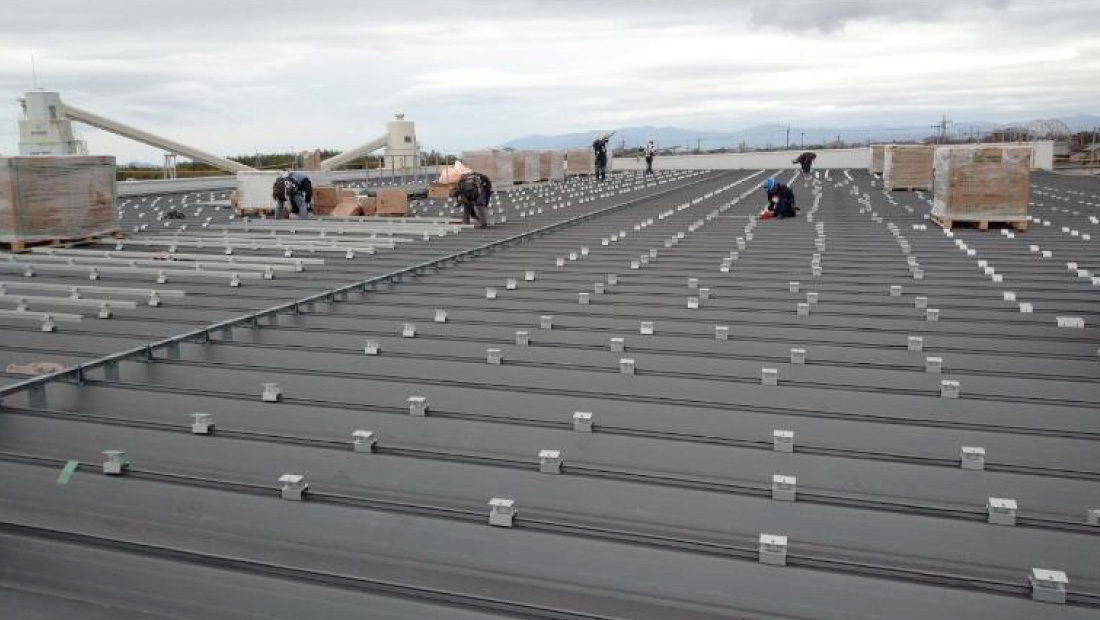
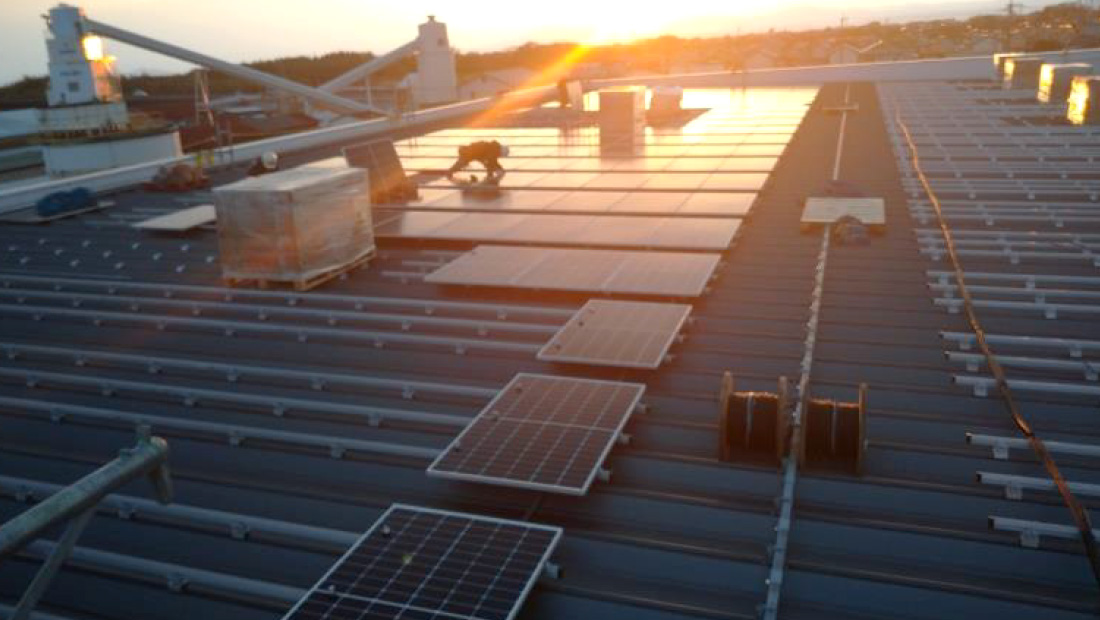
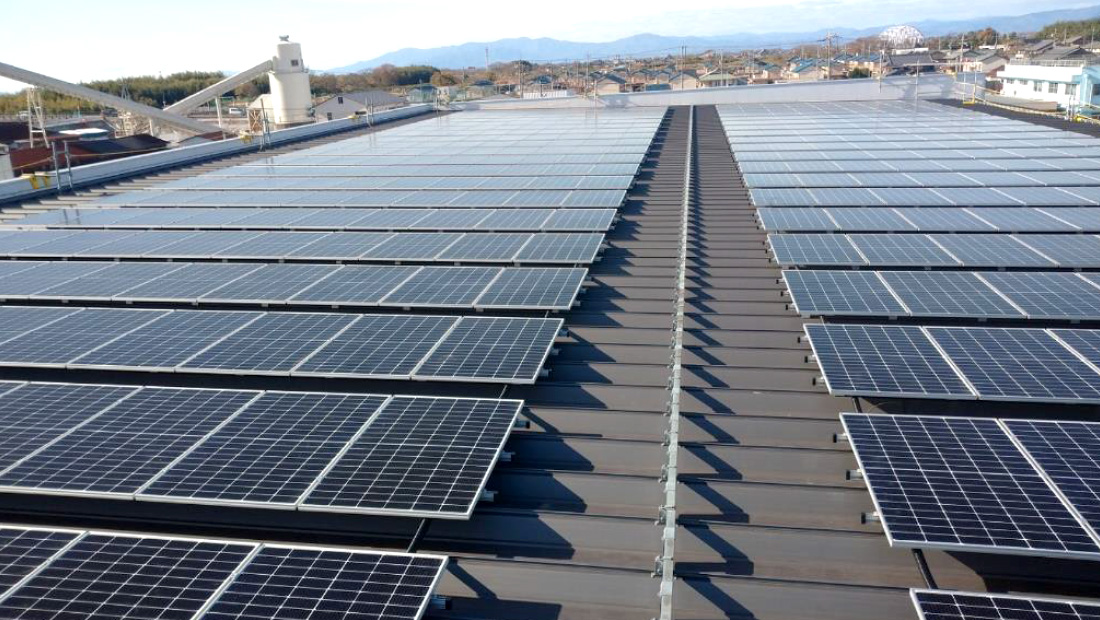
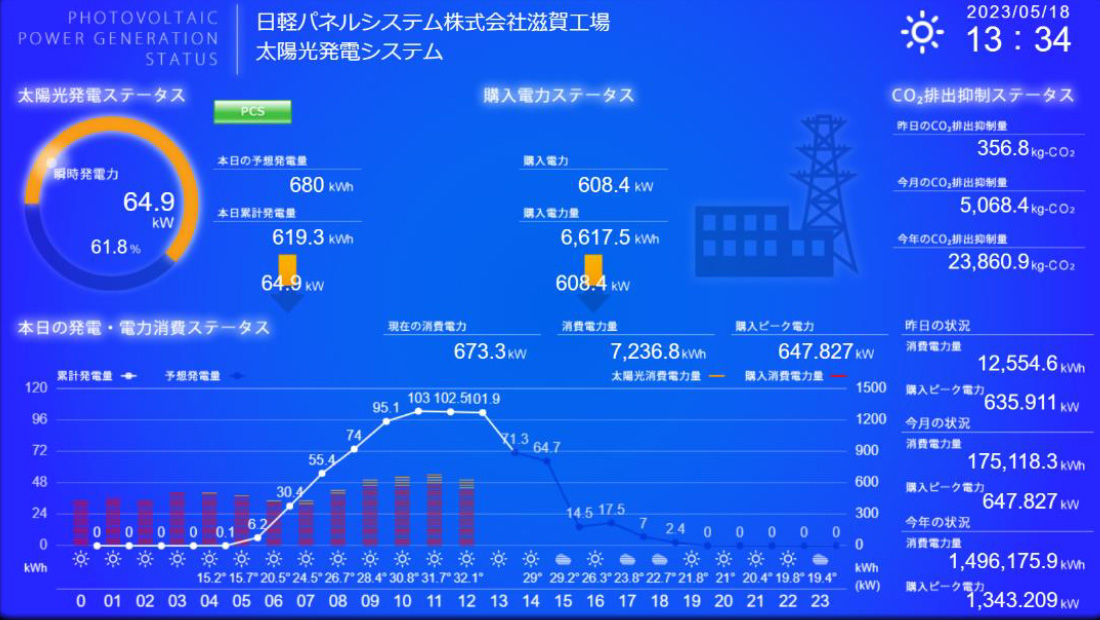
Solar power generation installed on the roof of Shimonoseki Plant No. 2
Solar power generation became operational on the roof of Shimonoseki Plant No. 2 in February 2025. The system is capable of generating up to 250kW of power, covering 25% of the electricity usage of the entire Shimonoseki Plant.
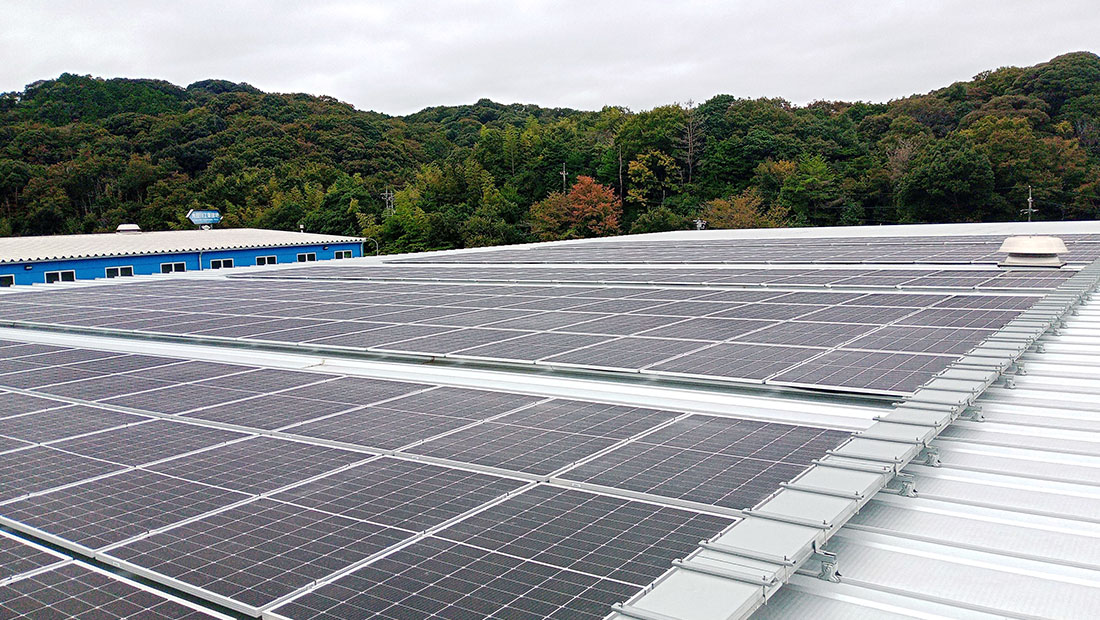
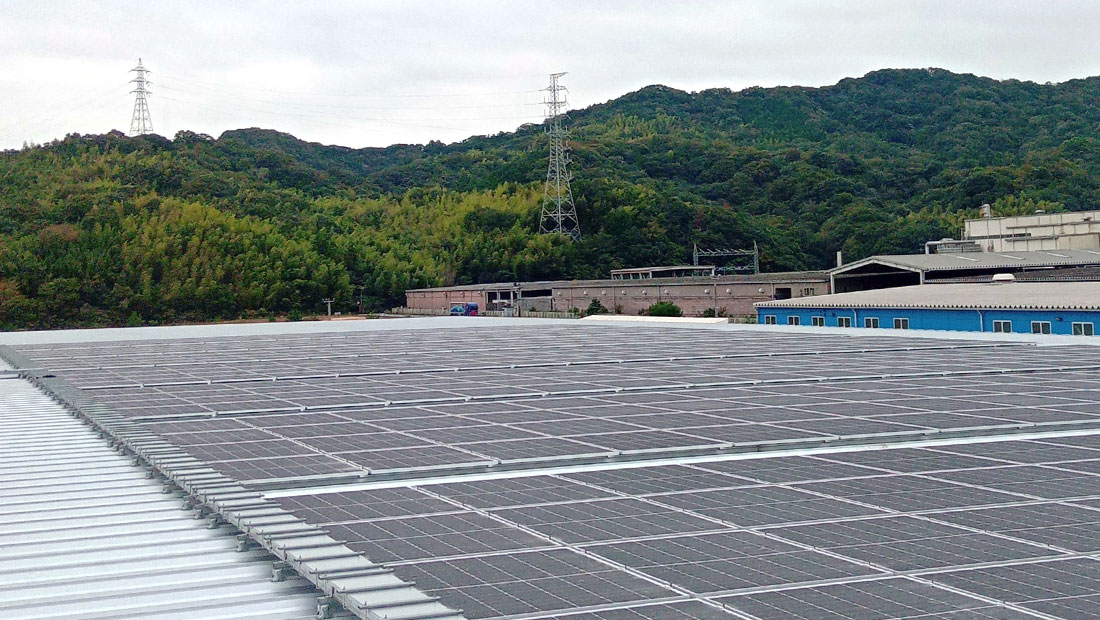